How to Protect Workers During Welding Fabrication
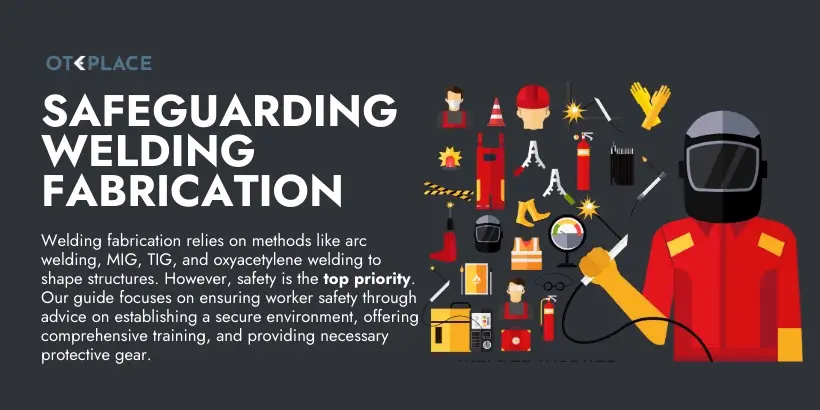
Welding fabrication, the process of joining metal pieces to create structures, relies on various techniques like arc welding, MIG, TIG, and oxy-acetylene welding. Skilled welders utilize these methods to craft anything from simple frameworks to intricate industrial assemblies. However, without proper precautions, this work can pose significant risks.
In this guide, we outline essential steps to safeguard workers during welding fabrication. We cover creating a secure work environment, providing thorough training, and supplying the necessary protective gear.
Explore our recommendations for welding protective gears
The Importance of Worker Safety in Welding Fabrication
Welding and metal fabrication environments pose several risks, ranging from exposure to hazardous substances to high heat exposure.
For example, certain welding processes such as tungsten inert gas welding emit dangerous gases that can result in respiratory issues and long-term health complications if adequate protection isn’t provided.
Additionally, the intense heat generated during welding techniques like stick welding or underwater submerged arc welding poses threat of burns and fires, making it vital to implement proper safety measures. Prioritizing worker safety not only safeguards your workforce but also maintains productivity and prevents costly accidents.
Safety Regulations for Welding Fabrication
In the United States, the primary authority overseeing worker safety in welding fabrication is the Occupational Safety and Health Administration (OSHA). However, beyond OSHA, various regulations and safety standards play pivotal roles in ensuring worker safety throughout the welding process.
Occupational Safety and Health Administration (OSHA)
OSHA is dedicated to establishing safety standards that safeguard workers from hazards in their workplaces. These standards cover a spectrum of concerns in welding fabrication, spanning from proper ventilation to ensuring the provision of adequate Personal Protective Equipment (PPE) and addressing electrical safety.
Additionally, it’s essential to recognize the significance of complying not only with OSHA regulations but also with minor, local, and specific standards. Such as:
ANSI Z49.1:2012 | The American National Standards Institute (ANSI) outlines safety in welding, cutting, and allied processes. It includes guidelines for selecting appropriate PPE for different welding applications. |
AWS (American Welding Society) | The AWS offers resources and fact sheets on safety and health in welding, which include recommendations for PPE usage. |
NFPA 70E | The National Fire Protection Association's NFPA 70E primarily focuses on electrical safety, while also addressing:
|
Manufacturer Guidelines | Follow the manufacturer's guidelines and recommendations for specific PPE, such as welding helmets, gloves, and respiratory protection. These guidelines often include information on proper use, maintenance, and replacement intervals. |
Local Regulations | Depending on your geographical location, additional regulations or standards set by local authorities or industry associations may apply. |
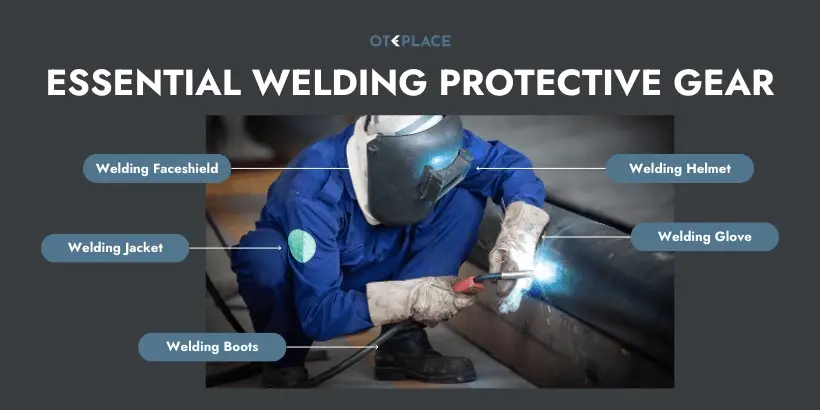
PPE for Welding Fabrication
Provide your workers with suitable Personal Protective Equipment (PPE) for welding fabrication and ensure they receive thorough training on its correct usage and upkeep.
Here's an overview of essential PPE items necessary for welding fabrication:
Welding Helmets | Face shield and welding helmets (note: can the link be opened in a separate tab) protect eyes and face from intense light and heat. |
Protective Clothes | Flame-resistant attire (leather or cotton) and covering skin from sparks, molten metal, and flames can keep employees protected. Long sleeves and pants should be used to cover exposed skin, while clothing should be free from oil, grease, or flammable substances. |
Gloves | Gloves protect hands from burns, sparks, and cuts. Provide heat–resistant materials to maintain dexterity. |
Respiratory Protection | Guards against harmful fumes and gases, where appropriate respirators or marks are required. |
Ear Protection | Earplugs or earmuffs can prevent hearing loss from loud noise levels. |
Foot Protection | Wearing safety boots or shoes with steel toes can safeguard feet from falling objects and heavy equipment. |
Remember to regularly inspect and maintain PPE to ensure its effectiveness regularly. Additionally, workers should be educated on the proper use and care of their PPE to maximize its protective capabilities.
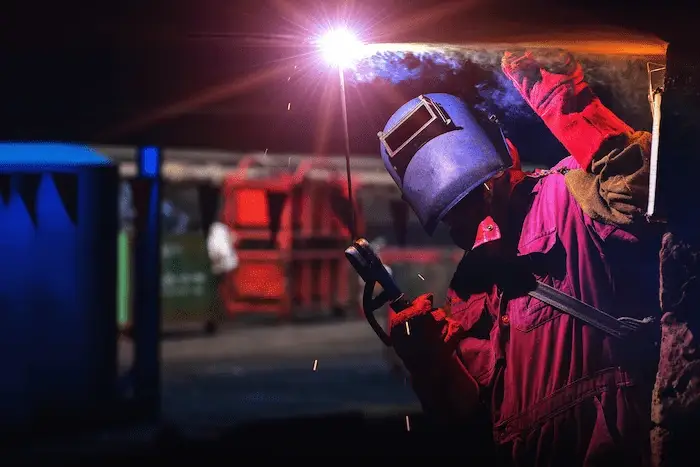
Welding Ventilation and Fume Control
Gas tungsten arc welding, proper ventilation and fume control are essential to protect workers from harmful fumes and gases. Inadequate ventilation can result in the accumulation of toxic substances in the work area, posing a significant risk to workers' health. Here are some key considerations for welding ventilation and fume control:
Local Exhaust Ventilation (LEV)
LEV systems are designed to capture and remove fumes and gases at their source, preventing them from spreading into the work area. These systems typically consist of hoods, ducts, and fans that pull the contaminated air away from workers. LEV systems should be properly designed, regularly maintained & inspected to ensure their effectiveness.
General Ventilation
General ventilation provides a continuous supply of fresh air to the work area. This helps dilute any remaining fumes and maintain a safe breathing environment. General ventilation can be achieved through fans, open doors and windows, or mechanical ventilation systems.
Fume Extraction Guns and Torches
Using fume extraction guns and torches can help capture and remove fumes directly at the welding point. These tools are particularly useful in confined spaces or situations where LEV systems may not be sufficient.
Proper Positioning of Workers
Workers should be positioned to minimize their exposure to welding fumes. This can include positioning themselves upwind of the fumes or using shields and barriers to divert fumes away from their breathing zone.
Regular monitoring of air quality and fume levels is essential to ensure ventilation systems work correctly. Provide workers with training on the hazards of welding fumes and the importance of proper ventilation.
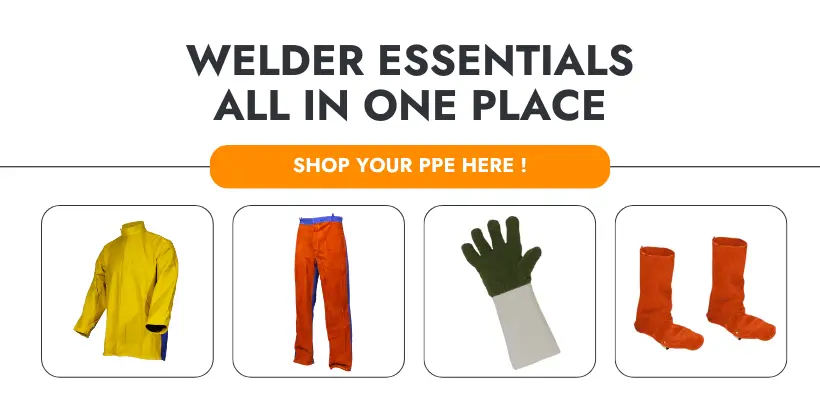
Fire Prevention and Safety Measures in Welding Fabrication
Fires and explosions are significant risks in welding fabrication due to the high temperatures involved and the potential presence of flammable materials. Here are some key fire prevention and safety measures for welding fabrication:
Proper Storage of Flammable Materials
Flammable materials, such as gases, solvents, and combustible liquids, should be stored in designated areas away from welding operations. These storage areas should be well-ventilated, equipped with fire extinguishers, and marked to prevent accidental ignition.
Fire Extinguishers and Blankets
Fire extinguishers should be readily available in the welding area, and workers should be trained in their proper use. Different types of fires may require different extinguishing agents, so have the appropriate extinguishers on hand. Fire blankets can also be used to smother small fires or wrap around a person if clothing catches fire.
Hot Work Permits
Before conducting any hot work, such as welding or cutting, obtain a hot work permit. This permit ensures that proper safety measures, such as fire watches and fire suppression systems, are in place to prevent fires and respond quickly in an emergency.
Clearing The Work Area
Before you start welding, remove any flammable materials, debris, or combustible substances from the work area. This helps lower the risk of sparks or molten metal causing nearby objects to catch fire.
Emergency Response Planning
Having a comprehensive emergency response plan in place protects workers in the event of a fire or other emergencies. The plan should outline evacuation routes, assembly points, and communication protocols. Regular drills should be conducted to ensure that workers are familiar with the procedures.
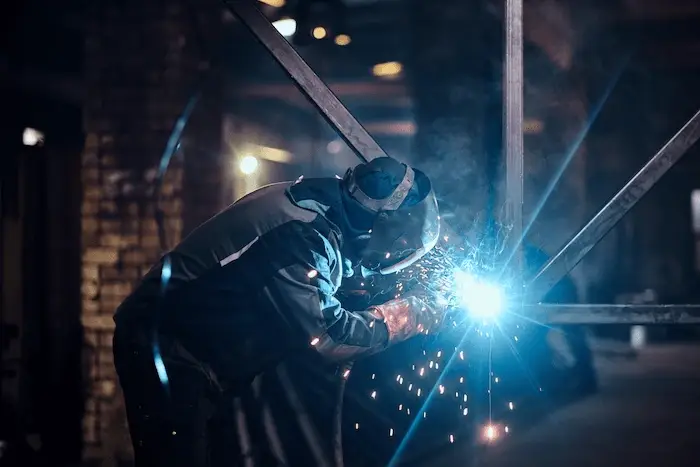
Proper Handling and Storage of Hazardous Materials in Welding Fabrication
Welding fabrication often involves working with hazardous materials, such as gases, solvents, and chemicals. Here are some key considerations for the handling and storage of hazardous materials:
Material Safety Data Sheets (MSDS)
MSDS provides detailed information about hazardous materials, including their physical and chemical properties, safe handling procedures, and emergency response measures. Have an MSDS readily available for all hazardous materials used in fabrication and welding.
Labeling And Signage
Hazardous materials should be clearly labeled, indicating their contents, potential hazards, and proper handling precautions. Additionally, signage should be posted in areas where hazardous materials are stored, indicating restricted access and emergency contact information.
Proper Storage Containers
Hazardous materials should be stored in approved containers specifically designed for their safe storage. These containers should be tightly sealed, labeled, and stored in well-ventilated areas away from heat sources or ignition points.
Segregation And Compatibility
Different hazardous materials may react with each other, leading to fire, explosions, or toxic gas release. Segregate incompatible materials and store them separately to prevent accidental mixing. This includes keeping flammable materials separate from oxidizing agents and acids separate from bases.
Spill Control and Containment
Adequate measures should be in place to control and contain spills of hazardous materials. This can include using spill containment pallets, absorbent materials, and spill response kits. Workers should be trained in proper spill response procedures to minimize the impact of spills.
Regular inspections and audits should be conducted to ensure compliance with handling and storage regulations. Provide workers with training on the safe handling and storage of hazardous materials and emphasize the importance of following proper protocols.
Ready to Start Protecting Your Business & Employees?
Prioritizing worker safety in welding fabrication prevents accidents and promotes a secure working environment. By following proper handling and storage practices for hazardous materials, providing comprehensive training and education, and fostering a culture of safety, businesses can significantly reduce the risk of workplace incidents.
Remember, worker safety is a shared responsibility. Employers, supervisors, and workers must all work together to create a safer and more secure workplace in welding fabrication. By implementing the tips and strategies outlined in this guide, you can take the necessary steps to prioritize worker safety and reap the benefits of a safer and more efficient welding fabrication process.