Different Types of Welding and Their PPE Requirements
Welding is fundamental across industries, enabling metal joining to create structures essential in construction, manufacturing, and maintenance. Mastering various welding types is key to selecting the right technique and equipment, ensuring structural integrity and efficiency in fabrication. Welding’s versatility makes it indispensable for building everything from skyscrapers to intricate machinery.
Each welding process offers unique characteristics and benefits, along with specific safety requirements to protect workers from hazards like heat, UV radiation, and fumes. Selecting PPE for welders is crucial to reduce these risks and ensure safe operations. This article explores different welding processes and PPE essentials for enhanced safety during welding tasks.
Table of Contents
-
1. Types of Welding Processes
-
2. Advanced Welding Processes
-
3. Importance of PPE in Welding
-
4. Training and Certification
-
5. Regular Equipment Maintenance
-
6. Ensuring Welder Safety Through Proper PPE and Equipment
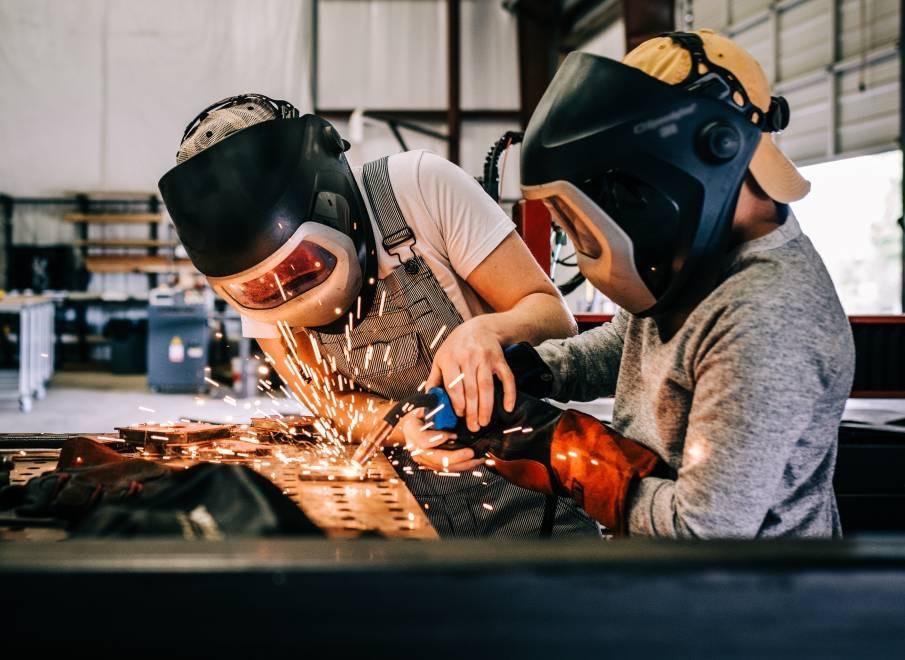
Types of Welding Processes
1. Shielded Metal Arc Welding (SMAW)
Also known as stick welding, shielded metal arc welding (SMAW) is one of the oldest and most widely used welding processes. Stick welding involves the use of a consumable electrode coated in flux. As the filler metal melts during the welding process, it produces a shielding gas that protects the molten weld from contamination.
Welders using SMAW should wear protective clothing made from flame-resistant materials, a welding helmet with appropriate shading, gloves, and safety boots. This gear protects against sparks, ultraviolet light, and high heat generated during the welding process.
2. Gas Tungsten Arc Welding (GTAW)
Gas tungsten arc welding (GTAW), or TIG welding, uses a non-consumable tungsten electrode to produce high-quality welds. An external shielding gas, typically argon or helium, protects the weld pool from atmospheric contamination. TIG welding is ideal for welding thin metals like aluminum and stainless steel.
For TIG welding, welders need a welding helmet, gloves, and flame-resistant clothing to shield against UV radiation and sparks. Additionally, a respiratory mask may be advisable when welding materials that produce harmful fumes.
3. Gas Metal Arc Welding (GMAW)
Gas metal arc welding (GMAW), or MIG welding (metal inert gas welding), uses a continuously fed wire electrode to create the weld. The arc welding process employs an external shielding gas to protect the molten weld from atmospheric contamination. GMAW is favored for its high welding speed and ability to weld thicker metals.
The PPE for GMAW is similar to that used for GTAW and SMAW, including a welding helmet, gloves, and flame-resistant clothing. Welders should also ensure proper ventilation in the workspace to avoid inhaling harmful gases.
4. Flux-Cored Arc Welding (FCAW)
Flux-cored arc welding (FCAW) is a variation of GMAW that uses a tubular wire filled with flux. The flux generates a shielding gas when heated, protecting the weld from contaminants. FCAW is particularly effective for welding in outdoor environments and on rusty materials.
Similar to other welding types, PPE for FCAW includes a welding helmet, gloves, and flame-resistant clothing. Due to the production of smoke and fumes, adequate ventilation is essential.
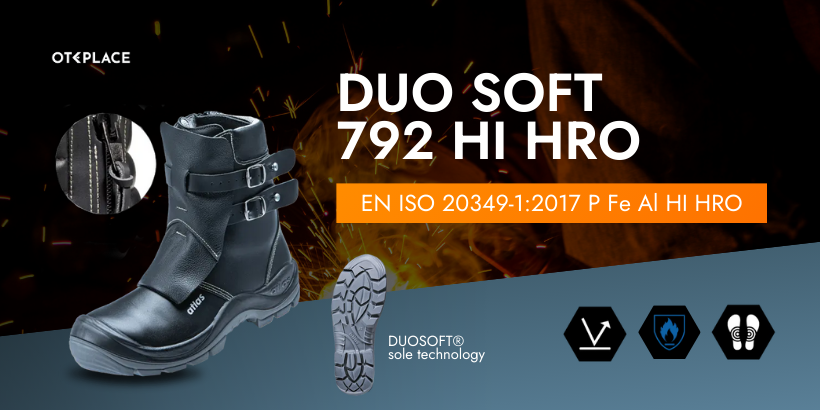
Advanced Welding Processes
Plasma Arc Welding (PAW) and Submerged Arc Welding (SAW)
Plasma arc welding (PAW) is an advanced welding technique that uses a constricted arc between a tungsten electrode and the workpiece. This process creates a high-heat plasma jet, allowing the precise welding of thinner materials. Often used in the aerospace and automotive industries, PAW produces strong, reliable welds.
In contrast, Submerged Arc Welding (SAW) is ideal for welding thicker materials, using a continuous wire electrode and granular flux to generate a high-quality weld. Both methods require protective gear, including a welding helmet with proper shading, gloves, and flame-resistant clothing.
Electron Beam Welding (EBW)
Electron beam welding (EBW) employs a beam of high-velocity electrons to create welds. This advanced welding process is performed in a vacuum, eliminating atmospheric contamination and allowing for the welding of thicker materials with high precision. EBW is commonly used in the aerospace and nuclear industries.
Due to the vacuum environment, PPE requirements for EBW may vary. However, protective clothing and face shields are still essential to safeguard against any potential hazards.
Laser Beam Welding (LBW)
Laser beam welding (LBW) is an advanced welding technique that uses a focused laser beam to melt and fuse materials. This method is known for its high welding speed and precision, making it suitable for welding thin materials and complex shapes. LBW is increasingly used in automotive and electronics manufacturing.
The PPE for LBW includes laser safety goggles, gloves, and protective clothing to prevent burns and exposure to laser light.
Atomic Hydrogen Welding (AHW)
Atomic hydrogen welding (AHW) is a unique process that uses a stream of atomic hydrogen gas to achieve extremely high temperatures. When hydrogen atoms recombine at the weld joint, intense heat is released, melting the metal. This method is primarily used for welding high-temperature metals like tungsten and is valued for creating high-quality welds with minimal contamination.
Due to extreme temperatures and hydrogen gas, welders must wear flame-resistant clothing, gloves, and face shields. Adequate ventilation is also crucial to disperse hydrogen gas and prevent risks from gas buildup.
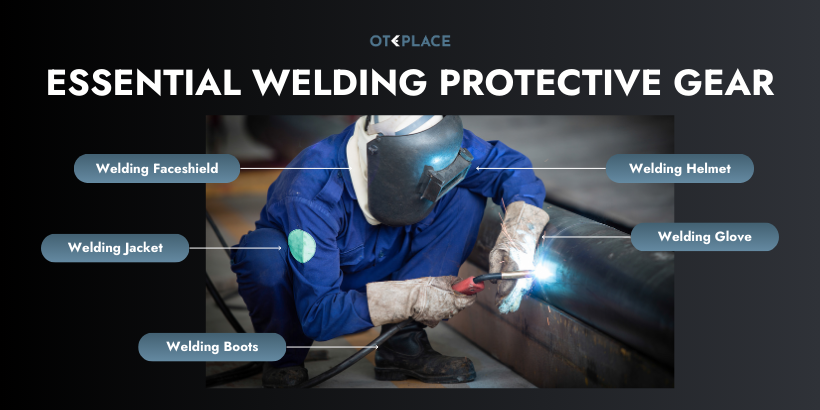
Importance of PPE in Welding
The use of welder personal protective equipment shields them from serious hazards like burns, harmful gases, and intense UV radiation from the welding arc. Proper PPE includes specialised clothing, helmets, gloves, and respiratory protection, each serving a specific protective function based on the welding process being performed.
Without the appropriate PPE, welders face heightened risks that could lead to severe, sometimes life-threatening injuries. Proper training in PPE use, along with consistent compliance, ensures that welders remain safe, even when working in high-risk environments and hazardous conditions.
Training and Certification
Proper training and certification are essential for welding technicians to ensure they fully understand welding techniques and crucial safety procedures. Training programs teach welders the properties of various materials and the correct joining methods, which are critical for producing high-quality welds and optimal results.
Certification programs also play an important role in promoting industry standards and safe practices. By completing certification, welders demonstrate their competency in specific techniques, increasing both their value as professionals and their adherence to established safety and quality standards.
Regular Equipment Maintenance
Maintaining welding equipment regularly is absolutely vital for both safety and operational efficiency in the welding process. Routine checks and servicing of welding machines, torches, and PPE ensure they function properly and safely, without compromising on quality or performance.
Scheduled maintenance helps prevent unexpected breakdowns and extends the lifespan of welding tools and equipment. For welders, this translates to consistent performance, fewer disruptions on the job, and an overall increase in both productivity and safer work conditions.
Ensuring Welder Safety Through Proper PPE and Equipment
Each welding type—from Shielded Metal Arc Welding (SMAW) to advanced processes like Electron Beam Welding (EBW) and Laser Beam Welding (LBW)—presents unique hazards that necessitate specialised personal protective equipment (PPE). Properly selected and worn PPE, such as flame-resistant clothing, welding helmets, gloves, and respiratory protection, serves as a critical defence against burns, UV radiation, toxic fumes, and other welding dangers.
In addition to PPE, comprehensive training and regular equipment maintenance are vital to creating a safe welding environment. Well-trained, certified welders who understand their equipment and safety practices contribute to higher-quality welds, operational efficiency, and reduced workplace accidents. By prioritizing safety measures and investing in high-quality PPE and equipment upkeep, industries can protect their welders and ensure a productive, safety-oriented workspace. This commitment to safety not only protects individual workers but also fosters a culture of resilience and reliability in welding operations.
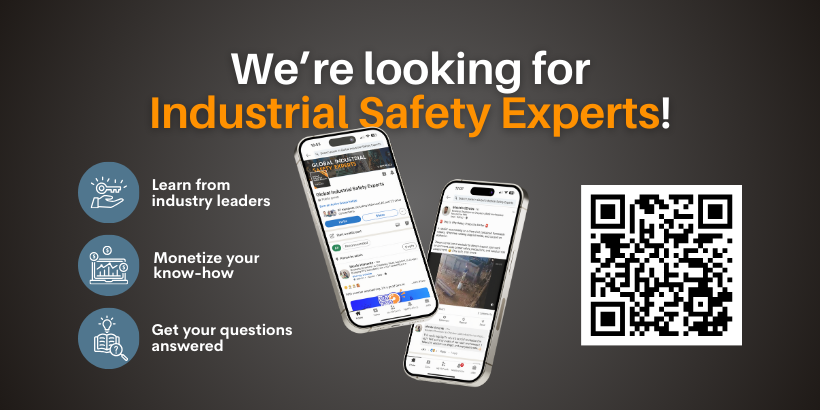