The risks involved in metal casting in the metallurgy and foundry industries
The metallurgy and foundry industries are two of the most critical areas of the manufacturing world. They provide essential raw materials for producing a variety of products, from pipe fittings to cars and planes. As such, it is important to understand the risks associated with metal casting in these industries — both for workers' safety and for product quality.
In this blog post, we will explore what metal casting is about and some of the potential risks and safety practices involved.
Understanding The Metal Casting Process
If you’ve ever seen a metal sculpture or intricate architectural detail, chances are it was produced using the metal casting process. Metal casting is an ancient process that has been used for centuries to create objects from molten metal. But what exactly is the metal casting process, and how does it work?
Metal Casting Basics
Metal castings begin with the creation of a pattern that will be used as a model for your finished product. Depending on the complexity of the design, this pattern may be made out of wood or plastic.
Once you have your pattern, you need to create a mold from it by using sand and heat-resistant materials like refractory bricks or ceramic shells. This mold serves as an outline for your desired object before you pour molten metal into it.
Once your mold is ready, you can begin to heat the metal until it reaches its melting point (this varies depending on what type of metal you are working with). You can then pour the liquid metal into your prepared mold and let it solidify. After cooling down and hardening, you can break open the mold to reveal your final product.
Depending on the type of material used for creating the molds (sand or ceramic), they may need to be broken away from the final product with hammers or sledgehammers before being recycled for future use.
This step requires extreme caution since there's always a risk of encountering hot spots while removing excess material from around the casted object — which can cause burns if handled without proper protective gear.
Post-Processing Of Metal Castings
Here, additional computer numerical control (CNC) machining operations are performed on finished castings so they meet customer requirements precisely. Machining such as drilling holes or adding threads may be required depending on what type of end product is desired by customers – whether that’s an engine part, weldment fixture, or something else entirely!
With post-processing completed comes inspection of both internal and external surfaces to ensure quality assurance standards are met before shipping out orders.
Potential Hazards Of Metal Casting
Though metal casting has been around for centuries, it remains one of the most dangerous processes in industrial production due to its high temperatures and contact with molten metals like aluminum, steel, brass, and bronze.
As such, safety protocols for occupational safety are crucial to protect workers from potential hazards such as burns caused by hot metals or toxic fumes created by heated chemicals during production.
Additionally, protective gear should always be worn when handling molten metals; this includes heat-resistant gloves and face shields to protect against splashes of hot liquid metals that could cause severe injury or death if not properly handled.
Something as simple as following instructions detailed on casting labels and safety data sheets or giving conscious attention to the warnings in the working vicinity can help avoid near-fatal incidents from occurring when melting metal and all through the molding process.
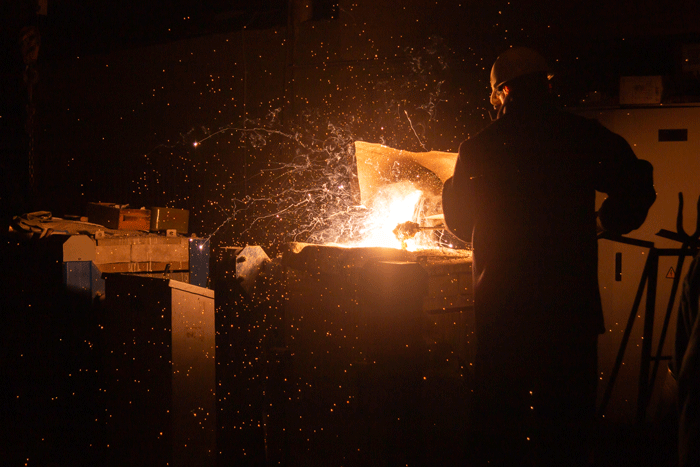
Risk Assessment And Hazard Identification
Conducting a thorough risk assessment and hazard identification for any metal-casting operation is essential to ensure the safety of everyone involved. Identifying potential sources of harm ahead of time allows you to take necessary precautions before beginning any work-related activities.
Additionally, this allows you to better manage your resources by ensuring that all necessary equipment is present before starting any operations and preventing any unexpected delays due to missing items or improper maintenance checks on existing ones.
Furthermore, conducting regular risk assessments also helps maintain good working relationships between employers and employees by making sure everyone understands their roles and responsibilities when it comes to safety guidelines.
What Is Hazard Identification?
Risk assessment is the process of identifying, assessing, and analyzing the risks associated with any given activity or project. It involves evaluating the likelihood of a particular event occurring as well as its possible impacts on resources, personnel, materials, processes, and products. After the risk assessment has been completed, it is then necessary to develop a plan of action to reduce or eliminate these risks if possible.
Hazard identification is an integral part of risk assessment as it helps identify potential sources of harm that can come from activities or processes being undertaken in an organization. It involves identifying potential hazards such as burns from hot metal surfaces, electrical hazards due to faulty wiring, or ergonomic risks from carrying heavy objects over long distances without proper protection.
The goal here is to identify all possible sources of harm that could arise during a project or activity so that appropriate steps can be taken beforehand to prevent them from occurring in the first place.
Creating Action Plans
After assessing each hazard for its risk level, action plans should be created to effectively address them. These action plans might include implementing safety protocols such as requiring employees to wear PPE when working with hazardous materials or installing new equipment that eliminates certain risks.
Hazard identification is an integral part of risk assessment as it helps identify potential sources of harm that can come from activities or processes being undertaken in an organization. It involves identifying potential hazards such as burns from hot metal surfaces, electrical hazards due to faulty wiring, or ergonomic risks from carrying heavy objects over long distances without proper protection.
It is also important that all employees are properly trained on modern casting safety protocols that are put into place so that everyone understands their role in keeping the workplace safe and secure well before any incident occurs.