Common Warehouse Hazards And Safety Tips For Protection
Working in a warehouse can be a rewarding experience, but it can also be dangerous. Accidents and injuries can happen at any time, and warehouse workers and managers need to prioritize safety to prevent them.
In this article, we'll explore the most common hazards found in warehouses, from slips and falls to heavy machinery accidents. We'll also offer practical tips for identifying and mitigating these risks.
Whether you're new to the industry or a seasoned pro, this guide will provide useful insights and best practices for keeping yourself and your team safe on the job.
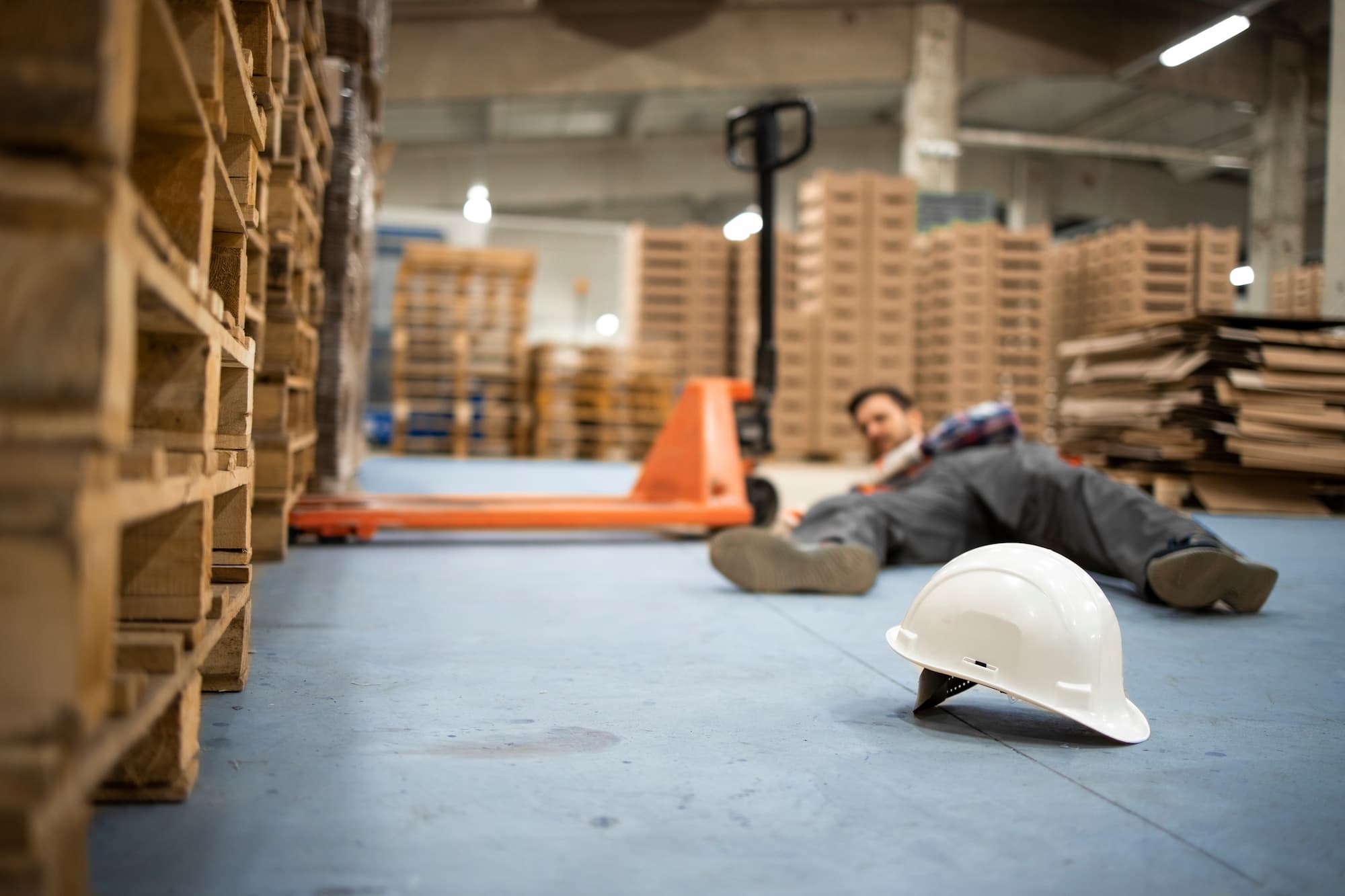
The Importance Of Warehouse Safety
As a business or a warehouse owner, you understand the importance of maximizing profits and minimizing costs. One area that can have a significant impact on your bottom line is warehouse safety. It's easy to overlook safety measures when you're focused on productivity and efficiency, but the consequences of neglecting safety can be severe.
Workplace accidents can result in lost productivity, medical expenses, lawsuits, and even fatalities. By prioritizing warehouse safety in your business strategy, you can protect your employees, your reputation, and your bottom line
Warehouse and worker safety should be a top priority for management. Safety measures not only prevent accidents and injuries but also increase productivity and efficiency in warehouse operations. Ensuring that everyone in the warehouse is properly trained and aware of potential hazards can make a significant difference in overall safety. Overall, prioritizing safety in a warehouse can help create a safe and productive workplace.
-
● Physical and Falling Hazards
Physical hazards are the most common type of hazard in a warehouse. They include slips, trips, falls, and collisions with objects. Slips, trips, and falls are often caused by wet or slippery floors, uneven surfaces, or poorly lit areas. Collisions with objects can occur when workers are not paying attention or when objects are not properly stored.
One of the leading causes of injury in warehouses is falls. They can occur from ladders, platforms, and elevated surfaces. To prevent these types of hazards, it's important to keep the warehouse clean and free of debris, ensure that floors are dry and slip-resistant, and provide adequate lighting.
Fall protection systems are one of the safest ways to prevent severe fall injuries or to block any falling objects in a warehouse.
Workers should also be trained to pay attention to their surroundings and avoid distractions while operating machinery or carrying heavy objects. Forklifts are a common sight in warehouses, but they can be dangerous if not used properly. To prevent accidents, it's essential to provide training to all forklift operators and to ensure that forklifts are well-maintained and in good working order.
-
● Chemical Hazards
Chemical hazards exist when there are hazardous materials stored in the warehouse. These materials can include cleaning products, pesticides, and other harmful substances that can cause burns, respiratory problems, and other health issues. To prevent chemical mishaps, hazard communication comes into play.
It's important to label and store hazardous chemicals and flammable materials properly, provide workers with proper personal protective equipment (PPE), and have a plan in place for spills or other emergencies. Employers must also provide respiratory protection to employees who may be exposed to dangerous airborne substances.
● Ergonomic Hazards
Working in a warehouse can be physically demanding, and employees may be at risk of ergonomic injuries such as strains and sprains. They are caused by repetitive motions or lifting heavy objects. These hazards can lead to musculoskeletal disorders, such as back pain or carpal tunnel syndrome.
To prevent ergonomic hazards, it's important to provide workers with ergonomic equipment, such as lifting aids and exoskeletons , and ensure that workers are properly trained on how to lift heavy objects safely.
Exoskeletons, also known as exosuits or wearable robots, are assistive devices designed to augment human capabilities by providing mechanical support during physically demanding tasks. These lightweight, wearable structures can significantly reduce the strain on the musculoskeletal system, offering substantial ergonomic benefits in warehouse environments. They can reduce the risk of musculoskeletal disorders, enhance endurance and productivity, and promote correct body posture. They can be utilized in tasks such as heavy lifting, order picking and packing, and logistics and material handling.
● Electrical and Fire Hazards
Electrical and fire hazards exist when there are exposed wires or improperly maintained electrical equipment in the warehouse. These hazards can cause electrical shocks, burns, or even fires.
To prevent electrical hazards, it's important to ensure that all electrical equipment is properly maintained and inspected regularly. Workers should also be trained on how to properly use electrical equipment and avoid exposing themselves to live wires.
Fire hazards can be taken care of with something as simple as sprinkler systems that can douse down the flames on immediate detection by the sensors. This provides some security against warehouse fires. Portable fire extinguishers are also quite invaluable to have at hand during a fire.
Common Warehouse Safety Hazards
There are several types of hazards, that can cause several workplace injuries, that warehouse owners and workers need to be aware of. These include physical, chemical, ergonomic, and electrical hazards.
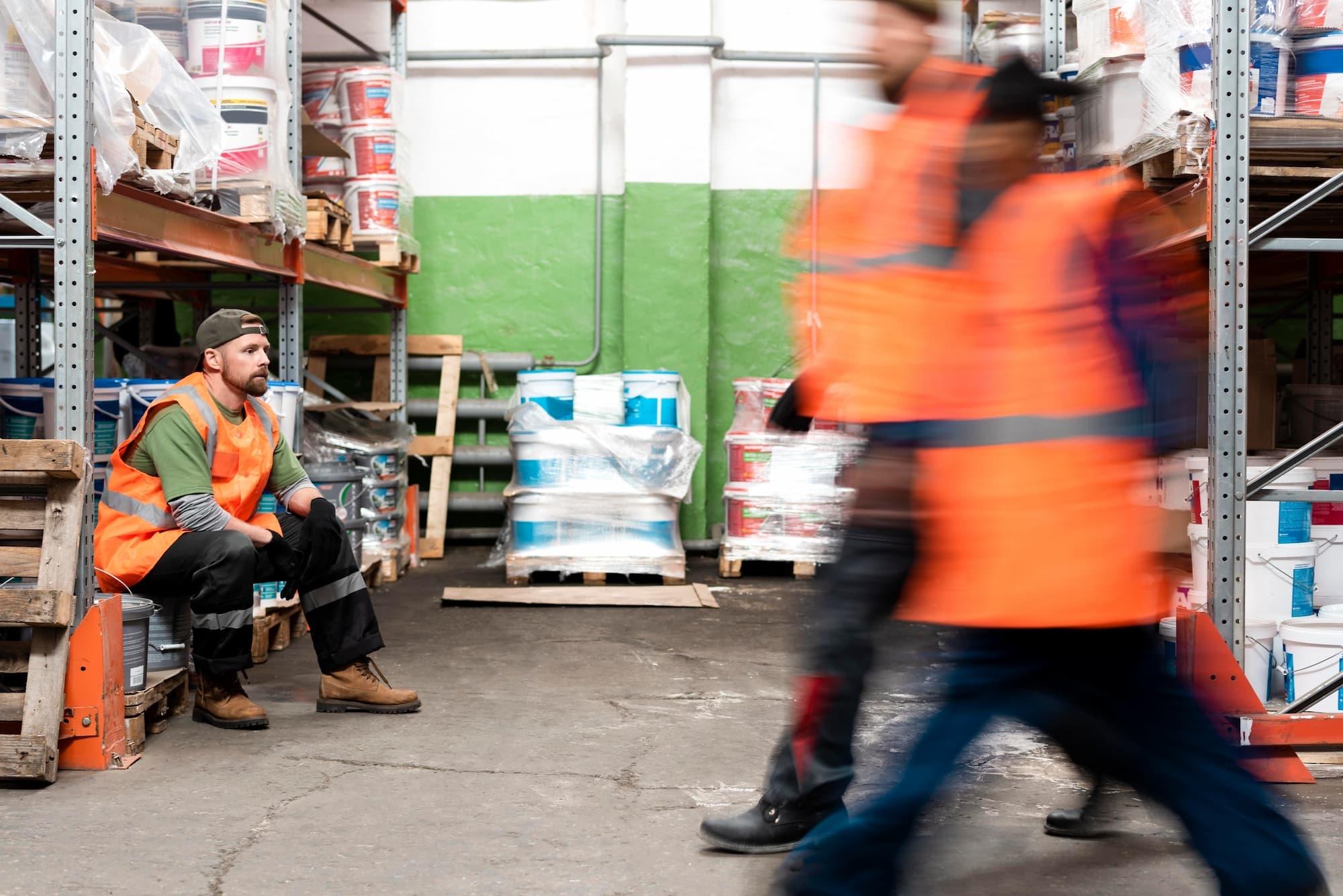
How To Identify And Assess Potential Hazards
Identifying and assessing warehouse hazards is critical to maintaining a safe working environment. It helps to prevent accidents, injuries, and property damage, which could result in costly legal battles and negatively impact the company's reputation. Here are some factors to help you identify and assess warehouse hazards.
● Regularly conduct safety audits
● Ask workers for feedback on potential hazards they have noticed
● Review incident reports identifying patterns or trends
● Observe warehousing workers to identify potential hazards in their work processes
Once potential hazards have been identified, it's important to assess their severity and likelihood of occurrence. This can be done by using a risk assessment matrix, which assigns a score to the likelihood and severity of a potential hazard.
Mitigation Strategies
Several strategies can be used to mitigate potential hazards, in turn avoiding serious injuries in the warehouse. They are as follows.
● Elimination: This involves removing the hazard entirely, such as replacing hazardous substances with non-hazardous ones or using automated equipment instead of manual labor.
● Substitution: This involves replacing hazardous chemicals or processes with a less hazardous one, such as using a less toxic cleaning product.
● Engineering Controls: This involves modifying the workplace or equipment to reduce the risk of a hazard, such as installing guardrails or using ventilation systems to control chemical fumes.
● Administrative Controls: This involves changing work practices or policies to reduce the risk of a hazard, such as implementing job rotations to reduce repetitive motions or limiting the amount of time workers spend in hazardous areas.
● PPE: This involves providing workers with the appropriate PPE, such as gloves, safety glasses, or respirators, to protect them from potential hazards.
Employee Training And Safety Culture
Proper training and a strong safety culture are critical to preventing accidents and injuries in the warehouse. It is mandatory to train workers on using equipment safely, identify potential hazards, and follow proper procedures.
To create a strong safety culture, management should lead by example and prioritize safety in all aspects of operations. Here are some best practices for training employees to help do their job safely:
● Conduct Regular Training Sessions
Conduct regular training sessions to ensure employees are aware of potential hazards and know how to mitigate them. Training should cover topics such as proper lifting techniques, safe use of machinery, and emergency safety procedures.
● Encourage Reporting
Encourage employees to report potential hazards and near-miss incidents. This helps to identify hazards early and prevent accidents.
● Involve Employees in Safety Planning
Involve employees in safety planning by asking for their input and feedback. This helps to create a culture of safety and encourages employees to take ownership of their safety.
Types Of Personal Protective Equipment
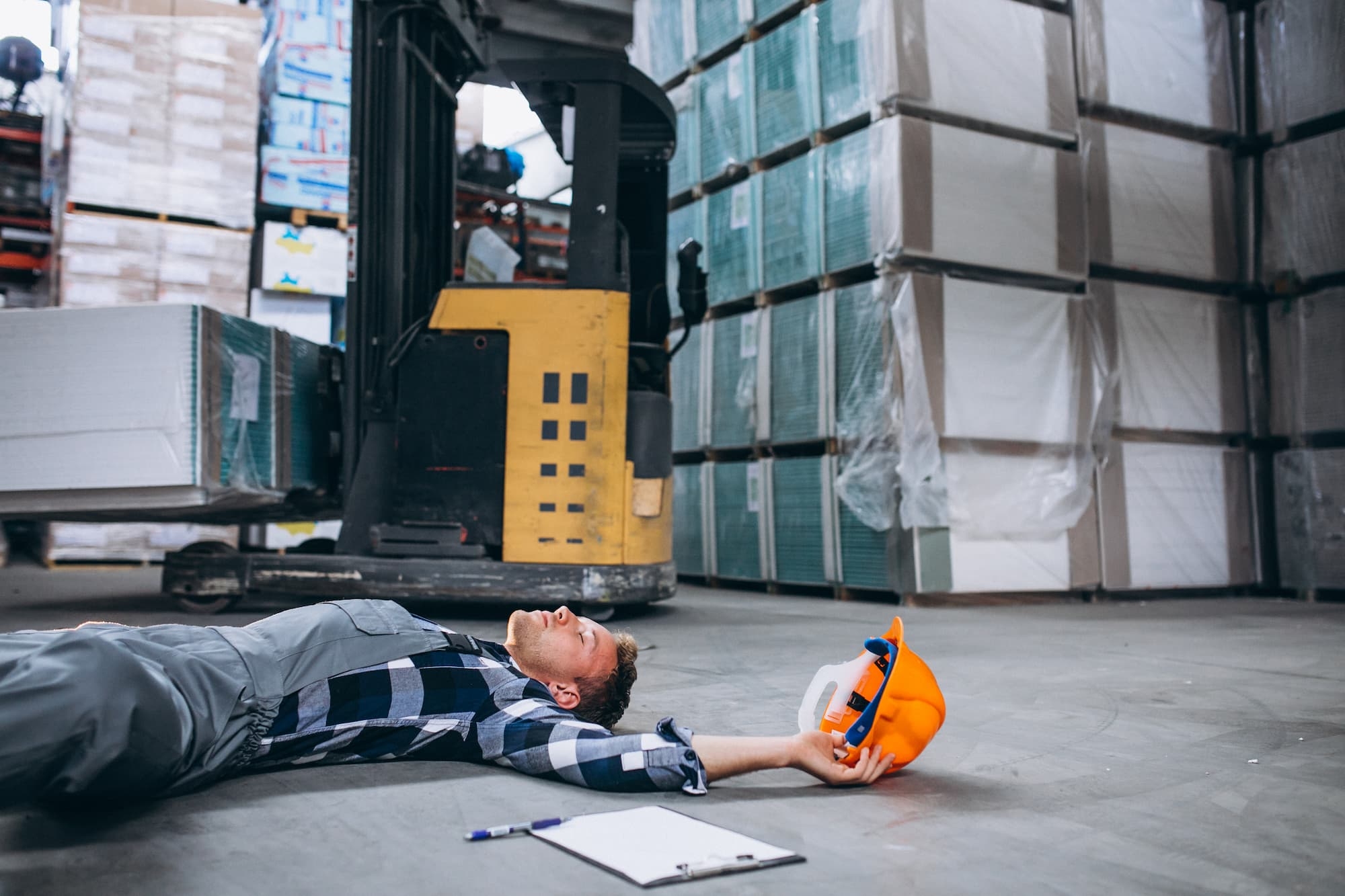
Personal Protective Equipment (PPE) is designed to protect workers from hazards that may cause harm while on the job. The type of PPE required will depend on the specific hazards present in your warehouse. Some of the common types of PPE include:
● Hard Hats: Hard hats are designed to protect the head from falling objects. They are essential for workers who are working under stacked goods or in areas where there is a risk of objects falling from above.
● Safety Glasses and Goggles: Safety glasses and goggles protect the eyes from flying debris, dust, and other particles. They are essential for workers who are operating machinery or working with chemicals.
● Respirators: Respirators protect workers from inhaling harmful chemicals, dust, and other airborne particles. They are essential for workers who are working with chemicals or in areas where there is a risk of airborne particles.
● Gloves: Gloves protect the hands from cuts, burns, and chemical exposure. They are essential for workers who are handling chemicals, sharp objects, or hot surfaces.
● Safety Shoes and Boots: Safety shoes and boots are designed to protect the feet from falling objects, slips, and electrical hazards. They are essential for workers who are working in areas where heavy machinery is in use.
Creating A Warehouse Safety Plan
The first step in creating a warehouse safety plan is to identify potential safety hazards and develop safety procedures and protocols. This involves conducting a thorough risk assessment of the warehouse to identify any potential safety hazards.
The safety procedures and protocols should be comprehensive and cover all aspects of warehouse operations. The procedures should be easy to understand and follow, and all employees should be trained on the procedures.
● Implementing Safety Equipment and Technology
The second step in creating a warehouse safety plan is to implement safety equipment and technology. There are various safety equipment and technology available that can help prevent accidents and injuries. For example, installing guardrails, safety nets, and safety barriers can help protect employees from falls and collisions.
Additionally, implementing technology such as automated guided vehicles (AGVs) and anti-collision systems can help prevent accidents involving forklifts and other heavy equipment. It is essential to regularly maintain and inspect all safety equipment and technology to ensure they are in good working condition.
● Regular Safety Audits and Evaluations
The third step in creating a warehouse safety plan is to conduct regular safety audits and evaluations. Safety audits are essential to identify any potential safety hazards and ensure that all safety procedures and protocols are being followed. Regular safety audits can help prevent accidents and injuries and ensure that your warehouse is a safe and secure environment.
During safety audits, you should review all safety procedures and protocols, inspect safety equipment and technology, and interview employees to ensure they understand and follow the safety procedures. Additionally, you should conduct regular evaluations of your safety plan to ensure it is up-to-date and effective in preventing accidents and injuries.
● Responding to Accidents and Emergencies
The fourth step in creating a warehouse safety plan is to develop procedures for responding to accidents and emergencies. Accidents and emergencies can happen despite your best efforts to prevent them. Therefore, it is essential to have procedures in place to respond quickly and effectively when they do occur.
The procedures should include steps to ensure the safety of employees, such as evacuating the warehouse or providing medical assistance. Additionally, the procedures should include steps to investigate the accident or emergency and implement measures to prevent it from happening again.
● Continuously Improving Your Warehouse Safety Plan
The fifth and final step in creating a warehouse safety plan is to continuously improve your safety plan. A safety plan is not a static document and should be updated regularly to ensure it is effective in preventing accidents and injuries.
Regularly review your safety plan and make changes as necessary to address any new safety hazards or changes in warehouse operations. Additionally, solicit feedback from employees on the effectiveness of the safety plan and make changes accordingly.
-
● Automated Safety Checklists
Automated safety checklists can be used to ensure safety protocols are followed consistently. They can be used to check for hazards, inspect machinery, and ensure personal protective equipment is being worn.
● Real-Time Location Systems
Real-time location systems can be used to track the movement of employees and equipment. They can be used to identify potential collisions and prevent them from happening.
● Virtual Reality Training
Virtual reality training can be used to train employees on how to use machinery and respond to emergencies. This helps to prepare employees for potential hazards without putting them in danger.
Using Technology To Improve Warehouse Safety
Technology can be implemented in safety procedures in several ways. Here are some examples: