Personal Protective Equipment in the Oil and Gas Industry
Fire and explosion hazards are major risks in the oil and gas industry. The safety of workers is critical to ensuring the success of an oil and gas company . Personal protective equipment (PPE) plays a crucial role in protecting workers from fire and explosion hazards.
Flame-Resistant Clothing
Flame-resistant clothing is a must-have for workers in the oil and gas industry. This type of clothing is designed to withstand high temperatures and prevent burns. Flame-resistant clothing can be made from a variety of materials, including cotton, wool, and synthetic fibers. Some types of flame-resistant clothing are also designed to protect against electric arcs and flash fire hazards. It's important to note that not all flame-resistant clothing is created equal, and you should always choose clothing that meets safety standards depending on your country or the country where the company operates
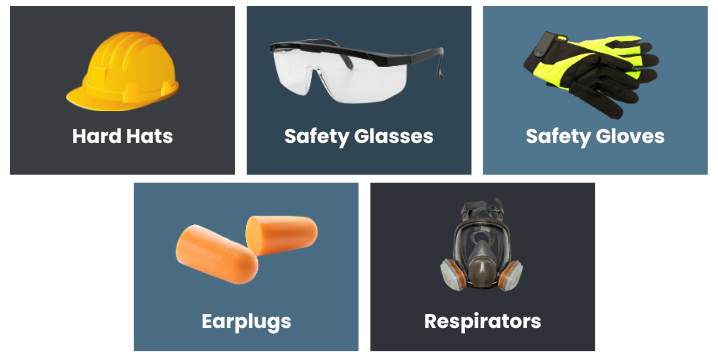
1. Hard Hats
Hard hats protect workers' heads from impact and penetration hazards. In the oil and gas industry, workers are often exposed to falling objects, which can cause serious head injuries. Hard hats protect against these injuries by absorbing the impact of falling objects and dispersing the energy throughout the helmet.
Hard hats can also be equipped with accessories such as chin straps and visors to provide additional protection. It is essential to choose a hard hat that fits well and meets safety standards.
2. Safety Glasses
Safety glasses protect workers' eyes from flying debris, liquid splashes, and dust. In the oil and gas industry, workers are often exposed to chemicals and particles that can cause eye injuries. Safety glasses must meet safety standards and should be worn at all times when there is a risk of eye injury.
3. Gloves
Gloves work by creating a barrier between the worker's hands and the hazards they are exposed to. The materials used in the protective gloves are designed to resist flames, high temperatures, and chemicals, which can cause burns and other injuries.
Flame-resistant gloves are designed to protect workers' hands from flames and heat. They are made of materials that can withstand high temperatures, such as leather and aramid fibers. Impact-resistant gloves are designed to protect workers' hands from impact injuries caused by objects such as hammers or wrenches. They are made of materials such as neoprene, PVC, or rubber. Chemical-resistant gloves are designed to protect workers' hands from exposure to hazardous chemicals. They are made of materials such as neoprene, nitrile, or PVC. Companies should choose the appropriate type of glove for the job and ensure that the gloves fit properly to provide maximum protection.
4. Earplugs
Exposure to loud noises is another hazard that workers in the oil and gas industry face. Hearing damage can occur over time due to exposure to high levels of noise. Earplugs help prevent this damage by reducing the amount of noise that reaches the ear.
There are two main types of earplugs: disposable earplugs and reusable earplugs. Disposable earplugs are made of soft foam or silicone and are designed to be used once and then thrown away. Reusable earplugs, on the other hand, are made of more durable materials, such as rubber or silicone, and can be used multiple times.
Earplugs work by fitting snugly into the ear canal and creating a seal that blocks out noise. The foam or silicone material used to make earplugs is designed to absorb sound waves, reducing the amount of noise that reaches the eardrum. Some earplugs also feature a noise reduction rating (NRR) that indicates how much noise they can reduce.
In the oil and gas industry, workers are exposed to high levels of noise from equipment and machinery, which can cause permanent hearing loss. Earplugs are crucial in protecting workers' hearing and preventing hearing loss. It is important to choose the appropriate type of earplug for the job and to ensure that the earplugs are properly fitted to ensure maximum protection. Workers should also receive proper training on how to use earplugs and the hazards they protect against.
5. Respirators
Respirators are designed to protect workers from inhaling hazardous substances such as dust and fumes. In the oil and gas industry, workers are often exposed to toxic chemicals and fumes that can cause serious health problems over time. Respirators help prevent these health problems by providing a barrier between the worker’s lungs and the hazardous substances
There are two main types of respirators: air-purifying respirators and supplied air respirators. Air-purifying respirators filter the air, removing contaminants before they are inhaled, while supplied air respirators provide fresh air from a remote source.
Air-purifying respirators come in different types, including:
-
a. Particulate respirators: These respirators are designed to filter out particulate matter, such as dust, smoke, and mist. They are often used in areas where workers are exposed to airborne particulates, such as drilling operations, sandblasting, and grinding.
-
b. Gas and vapor respirators: These respirators are designed to protect workers from inhaling gasses and vapors, which can be harmful to their health. They use different types of filters, such as activated charcoal filters, to remove specific gasses and vapors.
-
c. Combination respirators: These respirators combine the features of particulate respirators and gas and vapor respirators, providing protection against both particulate matter and airborne chemicals.
Supplied air respirators, on the other hand, provide fresh air from a remote source, such as an air compressor or a cylinder. They come in different types, including:
-
a. Airline respirators: These respirators are connected to a remote air source through a hose, providing a continuous flow of fresh air to the worker
-
b. Self-contained breathing apparatus (SCBA): These respirators provide the highest level of respiratory protection, as they are self-contained and do not require an external air source. They are often used in areas where the atmosphere is immediately dangerous to life or health, such as confined spaces.
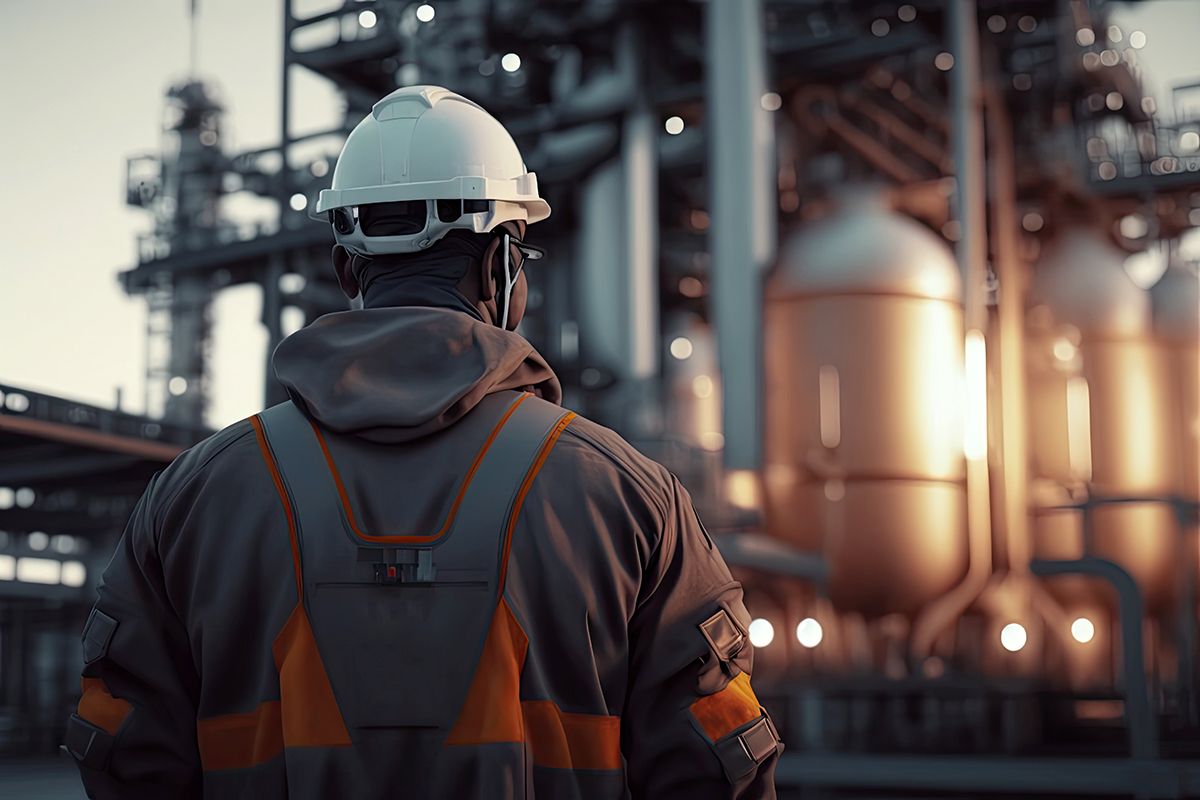
Emergency Response Plan for Explosion and Fire Safety in Oil and Gas Industry
What is an Emergency Response Plan?An Emergency Response Plan (ERP) is a comprehensive document that outlines the procedures and protocols to follow in case of an emergency. In the oil and gas industry, this plan should be designed to mitigate fire and explosion risks and should include detailed guidance on how to evacuate employees and deal with hazardous events. The response plan should also highlight the roles and responsibilities of each employee in the scenario of an emergency.
Importance of Having an Emergency Response PlanHaving an ERP in place helps to prepare your employees mentally and physically for potential emergencies. This planning process enables workers to feel more secure and confident in their roles, especially when in such an environment where the potential for such dangerous occurrences is high.
Moreover, effective emergency response plans have a profound impact on the legal and financial standpoint of your business. In the event a fire or explosion occurs, emergency personnel and the authorities will look to the company’s emergency response plan for guidance on how to handle the situation. Failure to comply with the regulatory requirements for workplace safety could leave your company open to substantial legal and financial repercussions.
What Should an Emergency Response Plan Include?
An ERP needs to include a checklist of key procedures and protocols, with roles, responsibilities, and communication channels outlined as listed below:
- Hierarchy of decision-making authority and a chain of command.
- Alert mechanisms to notify employees and emergency responders in case of an emergency.
- Evacuation procedures and designated meeting points.
- Firefighting and explosion mitigation plans, including access to fire extinguishers, fire suppression systems, and firefighting PPEs like aluminized suits.
- Ensure equipment maintenance, and sufficient stocks of appropriate personal protective equipment, first aid supplies, spill response, and firefighting equipment are available.
- Continuous updating and maintaining of the ERP to include new, applicable regulatory requirements and best practice industry standards.
Additionally, the emergency response plan should be reviewed, validated, and tested regularly to ensure every employee has a thorough understanding of the emergency response procedures and their roles in implementing them.
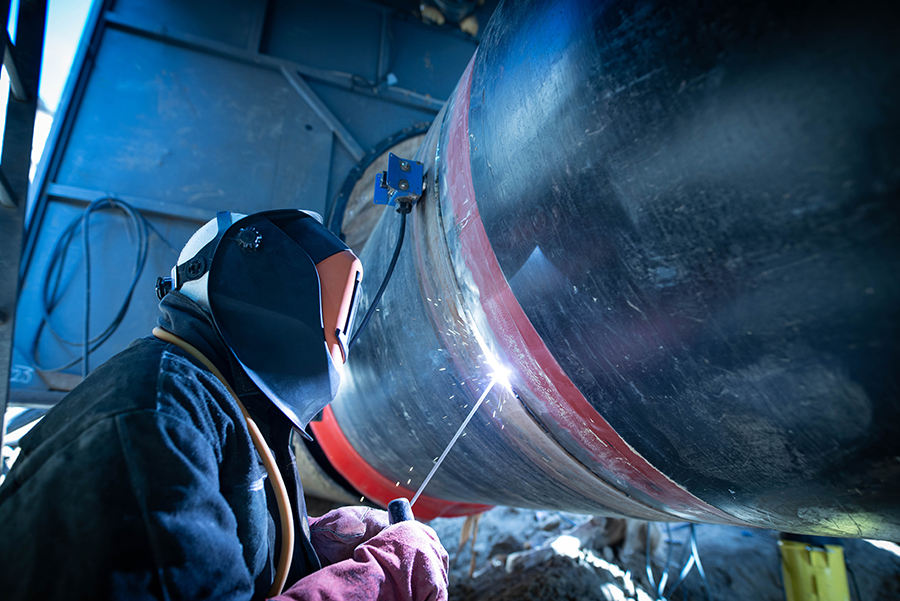
Final Thoughts On Minimizing the Risks of Fire and Explosion
-
The oil and gas industry is vulnerable to fire and explosion risks due to the flammable materials that are involved in the operations. To minimize risk, businesses must implement safety programs and practices, including identifying ignition sources and fuel sources, as well as ensuring proper ventilation in confined space areas.
-
Human error, natural disasters, equipment failure, and transportation can also increase the risk of fire or explosion incidents. Businesses must take measures such as training employees, backup plans for disasters, equipment maintenance checks, and securement protocols to reduce the risks and improve explosion and fire protection. Compliance with regulations and monitoring of regulatory updates should be an essential component of any company's safety measures.