5 Common Safety & Health Hazards in Manufacturing
As the manufacturing industry continues to evolve and grow, it is essential to prioritize the safety and health of workers. Various risks, from hazardous chemicals to heavy machinery pose dangers in the manufacturing environment. This article explores the common safety and health hazards in manufacturing and discusses effective strategies to safeguard workers.
Join us as we uncover the key safety and health hazards in manufacturing and delve into best practices for ensuring worker well-being and industrial success.
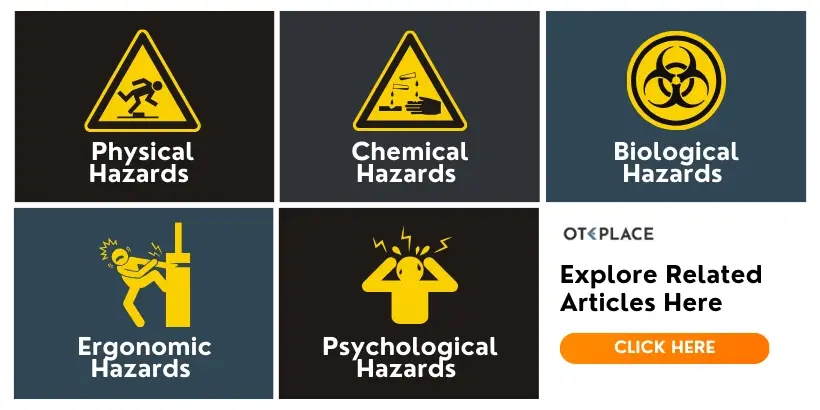
Table of Contents
1. Physical Hazards
2. Chemical Hazards
3. Biological Hazards
4. Ergonomic Hazards
5. Psychological Hazards
Importance of Safety and Health in Manufacturing
Ensuring the safety and health of workers in the manufacturing industry is non-negotiable. Manufacturing environments have hazards that can cause injuries or long-term health issues. By prioritizing safety, manufacturers protect their employees and enhance productivity and efficiency.
A safe work environment fosters employee morale and reduces turnover rates. When workers feel secure and protected, they are more likely to perform their tasks with confidence and focus. Moreover, preventing accidents and injuries lets manufacturers avoid costly downtime, medical expenses, and potential legal liabilities.
Common Safety Hazards in Manufacturing
The industry poses several safety hazards to workers. If not properly addressed, they can lead to accidents, injuries, and even fatalities. Here are the major but common workplace hazards in manufacturing companies:
Physical Hazards
Manufacturing workers face common physical hazards like slips, trips, and falls due to wet surfaces, clutter, or poor lighting, leading to severe injuries. Improper machinery use can cause accidents, such as being caught in moving parts or struck by falling objects. Noise exposure from machinery can result in hearing loss. Faulty electrical equipment can cause shocks, arc flashes, blasts, and explosions.
Chemical Hazards
Chemical hazards are significant in industries using solvents, acids, or toxic gases. Exposure can cause respiratory issues, skin irritation, and severe health problems like cancer. Flammable or reactive chemicals, if mishandled, can lead to fires or explosions.
Biological Hazards
Biological hazards are critical in sectors like food processing and pharmaceuticals, involving bacteria, viruses, fungi, or microorganisms. Poor hygiene, waste management, or inadequate PPE can spread infections. Pharmaceutical workers risk infection from live organisms, potentially releasing harmful pathogens into the environment.
Ergonomic Hazards
Ergonomic hazards stem from job physical demands, leading to musculoskeletal disorders. Repetitive tasks like lifting or operating machinery cause strain. Poor workstation design increases injury risk and discomfort, affecting long-term health and productivity.
Psychological Hazards
Psychological hazards, such as high stress, excessive workload, and poor communication, contribute to anxiety, depression, and burnout. Repetitive tasks and strict procedures can cause feelings of helplessness. Unfavorable physical conditions, like loud noises and extreme temperatures, add to stress and discomfort.
Precautions And Solutions for Employee Safety
With the potential hazards and risks involved in operating heavy machinery and working with chemicals, companies must take precautions and implement solutions to ensure the well-being of their employees. The following are a few ways in which you can practice safety for employees:
Protective Clothing
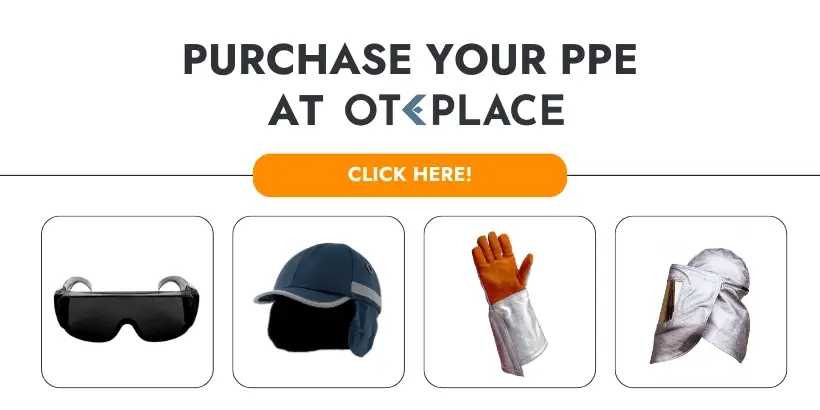
Protective clothing varies based on specific hazards in manufacturing facilities:
Chemical-Resistant Suits and Gloves:
Essential in environments with chemical exposure, these garments prevent hazardous substances from reaching the skin.Heat-Resistant Clothing:
Fire-Resistant Suits and gloves protect against high temperatures, reducing the risk of burns and thermal injuries.Contamination Prevention:
In industries like pharmaceuticals and food processing, cleanroom suits and food-grade attire minimize contamination in the production process.
Powered Industrial Machines
Powered industrial machines play a crucial role in increasing employee convenience and safety. These machines are designed to streamline workflow and reduce manual labor. This saves time and reduces the physical strain on employees, allowing them to work more comfortably and efficiently. These safety measures reduce the risk of workplace injuries and create a safer working environment for employees.
Machine Guarding
Machine guarding refers to using protective barriers or devices to prevent workers from contacting dangerous moving parts of machinery. One common solution for machine guarding is the use of fixed barriers. These physical barriers are designed to enclose hazardous areas of machinery completely.
Another solution for machine guarding is the use of interlocking guards. Interlocking guards are designed to stop or disable the machinery when the guard is opened or removed. This ensures the machine cannot be operated while workers access the hazardous areas.
Safety Training and Education
By providing proper training, employees are equipped with the knowledge and skills necessary to identify and mitigate potential risks in the workplace. They learn about the proper use of personal protective equipment (PPE), safe handling of machinery and equipment, and emergency response procedures. By educating employees about safety regulations, policies, and procedures, organizations can create a culture of safety in the workplace.
Routine Maintenance Activities
Identifying and mitigating equipment malfunctions is a key precaution that routine maintenance activities address. Over time, machinery and equipment in a manufacturing plant can wear out or develop faults that may compromise their functionality and safety. Regular maintenance checks allow early detection of such issues, enabling timely repairs or replacements.
Another important aspect of routine maintenance activities is the inspection and maintenance of safety devices. If not properly maintained, these safety devices can become ineffective or malfunction when needed the most.
Regulations And Standards for Safety in a Manufacturing Facility
Safety in a manufacturing facility is of utmost importance to protecting the employee's well-being and ensuring the smooth operation of the business. To achieve this, there are various regulations and standards in place that manufacturers must adhere to:
OSHA Regulations
One of the key regulations for safety in a manufacturing facility is the Occupational Safety and Health Act (OSHA) in many countries. OSHA sets forth guidelines and requirements for employers to provide a safe and healthy work environment for their employees. Regulations cover hazard communication, personal protective equipment, machine guarding, electrical safety, etc. By following OSHA standards, manufacturers can reduce the risk of accidents and ensure that their employees are protected from potential hazards.
ANSI Standards
There are also industry-specific standards that manufacturers must comply with. These standards are developed by organizations such as the American National Standards Institute (ANSI) or the International Organization for Standardization (ISO). For example, ISO 45001 is a standard that specifies requirements for an occupational health and safety management system. By implementing such standards, manufacturers can demonstrate their commitment to ensuring a safe working environment and continuous improvement in safety performance.
Environmental Safety Regulations
Manufacturers must also adhere to specific regulations related to environmental safety. This includes regulations on the handling and disposal of hazardous materials, emissions control, and waste management. Compliance with these regulations is crucial to protect the environment and prevent harm to employees and surrounding communities.
Regulations and standards for safety in a manufacturing facility play a crucial role in protecting employees and ensuring the smooth operation of the business. By complying with OSHA regulations, industry-specific standards, and environmental safety regulations, manufacturers can minimize the risk of accidents, injuries, and other hazards.
